Safety Clutter
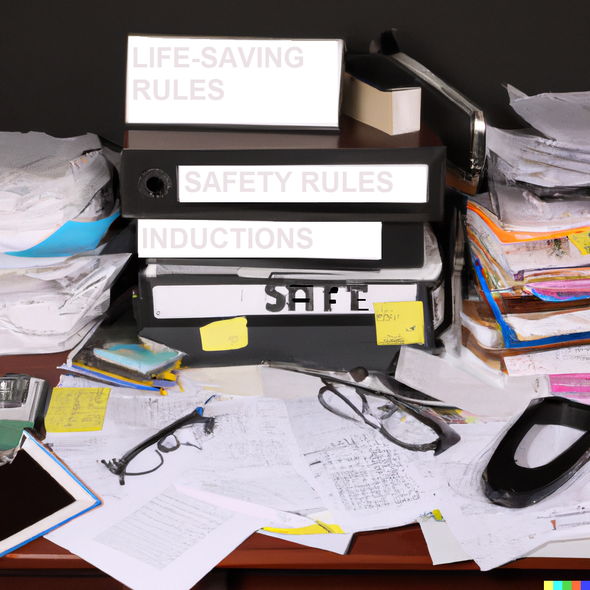
Safety Clutter: Assessing Redundant Practices and Improving Operational Effectiveness
Safety clutter = excessive safety procedures, documents, roles, and activities that are performed in the name of safety but don't actually contribute to operational safety
Clutter consists of activities that lack safety value, are redundant, or are applied in situations where their benefits aren't realized. For example, contractors have to go through multiple redundant safety inductions, wasting time and resources. This activity did not contribute to operational safety.
How does clutter come about?
When an organization (e.g., contractor) engages with multiple clients or within various units of the same parent organization, redundant processes for contractor safety pre-qualification, audits, and reports can be the result. When industries collaborate to solve safety problems, it often leads to the duplication of existing processes. For example, a safety culture survey implemented by multiple companies even after employees completed their company-specific safety questionnaires.
Also, when multiple management systems exist within the same organization, such as procurement, human resources, environment management, and project management, overlaps can exist in their safety-related requirements.
Thirdly, within a single system, excessive layers of checks or obsolete processes can exist, leading to forgotten or degraded purposes of these checks. Bureaucracy can result in unnecessary involvement across multiple layers for addressing safety incidents, i.e. if one level of a hierarchy is responsible for an issue, then every layer below that issue must also be involved, providing reports or delegating instructions.
Overextending safety measures hinders applicability and practicality
When rules or processes applicable in one situation are extended to multiple situations, they can become irrelevant or excessive. Sometimes rules are strictly applied without discretion, leading to overemphasis on safety measures even in non-risk situations, like enforcing full protective clothing for office workers outside hazardous areas. Applying rules intended for high-risk operational activities in non-relevant spaces or units within an organization to demonstrate a commitment to safety can become excessive. For instance, using safety warnings meant for hazardous areas in administrative contexts. Creating blanket rules to avoid case-by-case decision-making may lead to unnecessary restrictions and complexity. For instance, treating every manhole as a confined space, necessitating specific safety protocols even when unnecessary. Implementing safety practices tailored for inexperienced workers across the entire workforce, can disregard the expertise of experienced professionals, resulting in unnecessary restrictions or procedures. When good practices are excessively documented, this can lead to increased workloads, 'requirements creep,' and over-prescriptive processes that limit flexibility and adaptability. For example, formalizing workplace risk assessments with extensive forms and procedures that complicate the assessment process.
Accumulation challenges the streamlining of safety tasks
It's simpler to add or expand safety tasks than to remove them. Many triggers prompt the addition or expansion of safety work, while few opportunities exist for reduction. These asymmetries create a cycle where safety activities, once introduced, tend to accumulate over time, leading to increased complexity. Even attempts to simplify safety often result in more clutter rather than genuine reduction. Crises trigger rapid introduction of safety activities, often without ensuring long-term effectiveness. Organizations, even in already safe environments, add safety activities to demonstrate safety to stakeholders. The distinct role of safety professionals leads to a focus on safety-specific activities, sometimes divorced from operational work. Flexibility in setting safety rules under goal-based regulations leads to a significant increase in safety activities to meet perceived standards.
Factors leading to a continuous growth of safety clutter within organizations
Organizations react by quickly introducing new safety activities to regain control and assure safety. The need to demonstrate safety leads to excessive paperwork and administrative activities, seen as proof of safety. Safety professionals, focused on safety-specific tasks, create and perpetuate safety clutter to establish authority and relevance. The flexible standards under goal-based regulations create confusion and a subjective sense of 'doing enough,' leading to a proliferation of safety activities, often focused on defensibility rather than efficacy. These factors, while intended to enhance safety, paradoxically contribute to the accumulation of safety clutter within organizations, emphasizing the role of administrative work and the psychological need to demonstrate safety in perpetuating this clutter.
The negative impact of safety clutter on engagement and adaptability
Safety clutter undermines the employee's perception of safety rules' practicality, leading to a lack of voluntary engagement or initiative in safety-related activities. Employees often pay lip service to safety but lack a sense of ownership of safety measures. Safety clutter hampers adaptability by focusing excessively on predictability and standardization, reducing the variability in safe work practices. This reduction limits the ways to perform tasks safely, leading to creative but unsafe workarounds or rule-breaking when necessary. The excessive checking and auditing associated with safety clutter can erode trust within an organization. The emphasis on compliance shifts the focus from genuine safety concerns to mere adherence to rules and paperwork. Safety clutter imposes time and resource constraints, competing with operational work. This situation may inadvertently lead to compromising safety in favor of meeting deadlines or budgets.
Strategies for tackling safety clutter
Safety clutter can be tackled by encouraging open discussions challenging the value of specific safety practices without undermining the overall safety philosophy. Introducing the term "clutter" facilitates this conversation. Organizations can identify clutter by directly asking workers about redundant safety activities. Testing the consequences of stopping each activity can help identify and remove unnecessary clutter. Framing clutter removal as a research problem encourages evidence-based decision-making. It helps organizations evaluate the purpose and effectiveness of safety activities. Safety professionals play a crucial role in clutter removal by managing external demands, promoting leadership styles focusing on evidence-based practices, and adopting a reflective, evidence-based approach themselves.
Ref.
Rae, A.J., Provan, D.J., Weber, D.E., Dekker, S.W.A. (2018), Safety clutter: the accumulation and persistence of ‘safety’ work that does not contribute to operational safety, in: Policy and Practice in Health and Safety, Volume 16, 2018 - Issue 2, Pages 194-211.